Process of Pet Plastic Bottles Manufacturers and its uses
Have you ever looked at the bottom of a plastic bottle or jar to discover what it is composed of? There's a good possibility you've come across one manufactured of polyethylene terephthalate. Pet Plastic Bottles Manufacturers is durable, resistant to breakage, and may be as transparent as glass bottles or jars. PET is a fantastic material choice for a variety of businesses. Strength and durability, intensity ratio, impact resistant qualities, and cheap product cost make it a viable option for disposable product packaging.
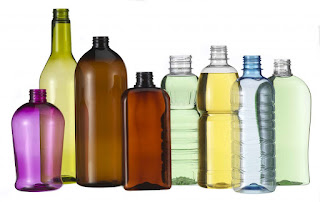
PET is appropriate for plastic bottles
PET is a great suggestion for plastic bottles due to its unequalled intensity ratio, cost benefits, and transit savings when compared to glass competitors, as well as its record of success for consumer product performance and quality.
Everything that you need to know about PET plastic bottles Wholesale is designed from the beginning of the production process to be a tough, yet malleable material that can be used in a variety of plastic glass containers.
It is vital to note where each bottle is thoroughly tested and monitored to ensure that safety requirements are met. We may have safe recycled plastic containers that conserve energy during manufacture, are cost effective, recyclable, and sustainable by employing polymers such as PET.
Plastic Material Is It Fully secure?
Many food and beverage products are packaged safely in PET plastic. PET plastic has been designated as safe for food and beverage contact by the FDA and other regulatory agencies throughout the world for more than 30 years.
One of the most common public worries has been the "profiting" of pathogens from plastic bottles into the items people consume. The FDA tests for the transfer of plastic components and other contaminants to the liquid contents of the bottle as part of its evaluation, which has been found to be within acceptable guidelines.
Molding Bottles Should Be Reheated and Blown
Compression casting is the first stage of a conventional two-step Reheat and Blow Machine (RBM) bottle production process. Plastic pieces are injection moulded in the cylinder of an injection moulding process, where heat and indeed the shredding action of a feed screw melt the plastic. The plastic is then pumped into moulds with many cavities, where it takes on the structure of elongated, small tubes.
These tubing, known as parisons, often feature the formed necks and screws which will be used to cover the upcoming bottles. Because PET parisons, or pre-forms, are significantly more compact than fully formed bottles, they are readily delivered to bottling operations.
The parisons are fed into a conveyor and processed through an approach when it comes during the re-heat process, which orients the parisons for injection into the blow moulding machine.

Bottles Made via Injection Blow Moulding
Other bottle technology advancements combine parison formation and blow moulding into a single constant process. A continuous extrusion technology, in which an extruder continually produces a parison, is one such mechanism. The parison develops vertically in the extrusion blow moulding process, and its wall thickness is controlled by adjusting the size of the opening within which the extrusion and injection extrudes.
Mould halves are closed over the hanging parison and sent to the blow moulding station, where the bottle is created as stated in the 2nd section of the RBM procedure. Modifying the minimum thickness solves the possibility of non-uniformity of the overhanging parison, that might otherwise extend the hot and somehow still part.
The mould must be cooled fast so that the freshly created component is designed properly. There are multiple indirect cooling methods that can successfully cool the mould and the plastic. Water can be sent through pipes encircling the mould, cooling it and the plastic indirectly. Direct techniques involve directly applying pressurised air or carbon dioxide to the mould and plastic. Contact us now.
Comments
Post a Comment